The Top 3 Trends in API Manufacturing
You need to know about!
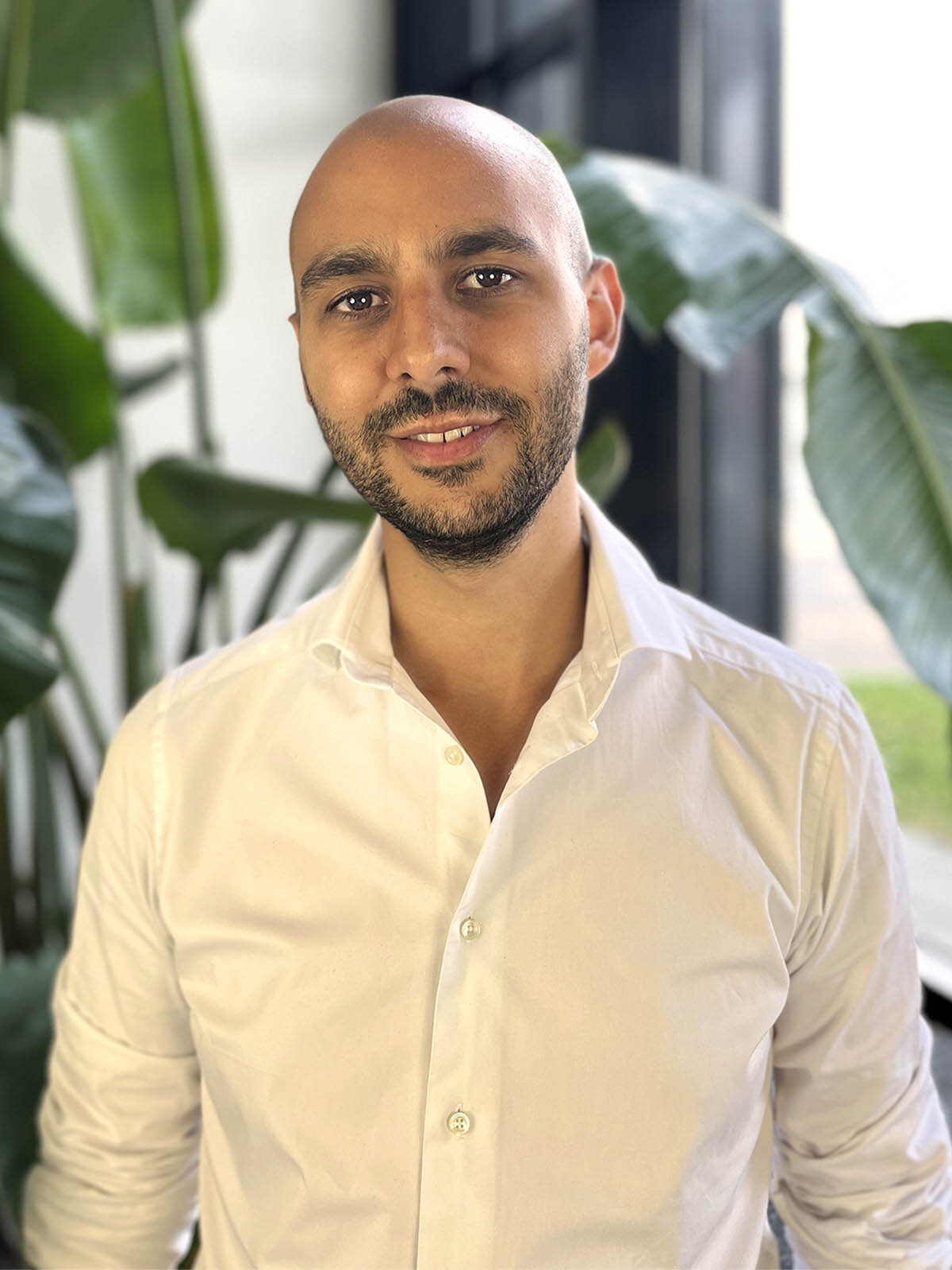
Ammar Badwy| Posted on May 18, 2023
The landscape of pharmaceutical manufacturing is continuously evolving, driven by advancements in technology, changing market demands, and the need for increased efficiency and quality. Within this dynamic environment, Active Pharmaceutical Ingredients (APIs) manufacturing is undergoing significant transformations, with new trends shaping the industry’s future.
Whether you’re a pharmaceutical professional, a healthcare provider, or simply curious about the latest developments in the field, understanding these trends is essential to stay ahead of the curve and harness the potential for innovation.
In this article, we will explore the top three trends in API manufacturing that are revolutionizing the industry and redefining how medications are produced. From the integration of advanced automation and robotics to the adoption of continuous manufacturing techniques and the rise of personalized medicine, these trends have the potential to transform the pharmaceutical manufacturing landscape and impact patient care.
1. Advanced Automation and Robotics: Enhancing Efficiency and Quality
Automation and robotics have significantly transformed various industries, and API manufacturing is no exception. The integration of advanced automation technologies in manufacturing processes brings numerous benefits, including enhanced efficiency, improved quality control, and increased productivity.
Robotic systems can perform repetitive tasks with precision, reducing the risk of errors and contamination. Automated systems can handle complex processes, such as formulation, weighing, and dispensing, with greater accuracy and consistency, leading to better product quality and reduced batch variations. Moreover, automation enables real-time monitoring and data collection, facilitating process optimization and rapid decision-making.
Additionally, robotics can be applied to hazardous operations, ensuring the safety of workers and minimizing exposure to toxic substances. By automating certain tasks, companies can also optimize resource allocation and streamline production, resulting in cost savings and faster time-to-market.
2. Continuous Manufacturing: Streamlining Production and Enhancing Flexibility
Continuous manufacturing is emerging as a transformative trend in API production, replacing traditional batch manufacturing methods. Unlike batch manufacturing, which involves sequential steps with pauses in between, continuous manufacturing operates as a continuous flow process, allowing for seamless production without interruptions.
This trend offers several advantages over batch manufacturing. First and foremost, continuous manufacturing reduces production time significantly, as there is no need for equipment cleaning and changeovers between batches. This results in increased overall productivity and faster delivery of APIs to the market.
Moreover, continuous manufacturing enables greater process control and monitoring, leading to improved product quality and consistency. The real-time monitoring of critical parameters allows for immediate adjustments and early detection of any deviations, minimizing the risk of product failures and ensuring regulatory compliance.
Continuous manufacturing also offers enhanced flexibility, allowing manufacturers to respond quickly to changing market demands. With the ability to adjust production volumes on the fly, companies can optimize resources and reduce waste, making API manufacturing more cost-effective and environmentally sustainable.
3. Personalized Medicine and Modular Manufacturing: Tailoring Treatments to Individuals
Personalized medicine, also known as precision medicine, is revolutionizing healthcare by tailoring treatments to individual patients based on their genetic makeup, lifestyle, and other factors. API manufacturing is adapting to this trend through modular manufacturing approaches that enable the production of smaller batches and customized therapies.
Modular manufacturing involves the use of smaller, self-contained manufacturing units that can be easily configured and reconfigured to produce different APIs. This flexibility allows for efficient production of personalized medicines, as manufacturers can adapt quickly to changing treatment requirements and produce smaller quantities without compromising cost-effectiveness.
Furthermore, modular manufacturing facilitates the integration of advanced technologies, such as 3D printing and continuous flow reactors, enabling the production of complex APIs with greater precision and control.
Personalized medicine and modular manufacturing also have the potential to optimize drug development processes. By manufacturing smaller batches, companies can conduct more rapid clinical trials, accelerate the introduction of new therapies to the market, and reduce the overall cost and risk associated with drug development.
Conclusion
API manufacturing is undergoing a transformative phase, driven by advanced automation and robotics, continuous manufacturing, and the rise of personalized medicine.
These trends offer exciting opportunities for pharmaceutical companies to enhance efficiency, improve product quality, and meet the evolving needs of patients and healthcare providers. Embracing these trends requires investment in cutting-edge technologies, collaboration between industry stakeholders, and a proactive approach to innovation
By staying abreast of these trends and adopting them strategically, pharmaceutical manufacturers can position themselves at the forefront of the industry, ensuring sustainable growth and delivering breakthrough therapies to patients worldwide.
Check out all other blogs here!